Customer Story
Sun Chemical
Sun Chemical is a supplier to the graphic arts industry and, together with its parent company DIC, the world’s largest manufacturer of printing inks. Using Icinga 2, they redesigned and upgraded their corporate infrastructure monitoring.
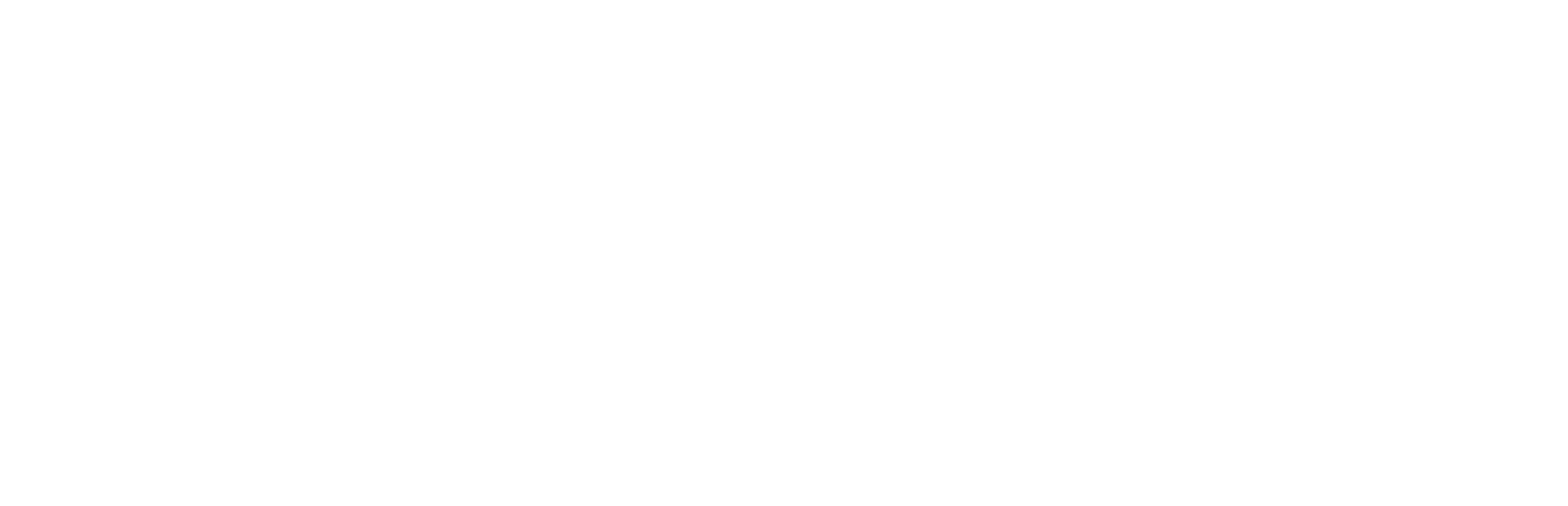
Sun Chemical has more than 200 years of color expertise. Their customers are global brands and retailers of various branches. The Coca Cola Red: that’s Sun Chemical. With close to 10.000 worldwide trademarks and over 3.000 granted patents in its history, Sun Chemical takes pride in producing solutions tailor-made to meet the individual needs of their customers.
Their mission: bring color to the world. Their monitoring: Icinga.
Since 2017 Sun Chemical is using Icinga 2 to monitor their server and network infrastructure. Since 2022 Sun Chemical is an Icinga support customer.
Sun Chemical, a member of the DIC Group, is a leading producer of packaging and graphic solutions, color and display technologies, functional products, electronic materials, and products for the automotive and healthcare industries. Together with DIC, Sun Chemical is continuously working to promote and develop sustainable solutions to exceed customer expectations and better the world around us. With combined annual sales of more than $8.5 billion and 22,000+ employees worldwide, the DIC Group companies support a diverse collection of global customers.
Sun Chemical Corporation is a subsidiary of Sun Chemical Group Coöperatief U.A., the Netherlands, and is headquartered in Parsippany, New Jersey, U.S.A. For more information, please visit our website at www.sunchemical.com or connect with us on LinkedIn, Instagram or Twitter.
The Challenge
A fresh Start for a Global Player
Sun Chemical has grown through various acquisitions and is present all over the globe. Just recently the company bought a division of the German chemical group BASF.
A couple of years ago, the company decided to redesign their monitoring and install a process that would guarantee that all their server infrastructure is inspected by the same basic set of monitoring checks.
This was around the same time that Alex Clark got hired as IT Specialist Active Directory & Monitoring at Sun Chemical. Alex Clark’s monitoring challenge was quite a journey – first, to gain knowledge about Sun Chemical’s processes, second, to figure out what kind of monitoring could fit a global player with many business units, divisions and IT departments. And third, it was about getting the whole organization on board.
Icinga 1 was the monitoring system they used at that time, and since that was not state-of-the-art anymore and already out of support, the company decided to upgrade to Icinga 2.
The Solution
High availability Setup
Sun Chemical has two datacenters, one at the US East Coast and one at the West Coast. The monitoring team runs two Icinga Masters for those two sites and for high availability. With the Icinga Module for vSphere it’s easy to get a detailed overview for a VMware cluster.
At the moment, Sun Chemical is migrating parts of its infrastructure up to Microsoft’s public cloud Azure. “We are in two different regions in Azure, and we put two Icinga Satellites in each region for high availability and to monitor all the Icinga clients in this region. With the two Icinga Masters we run a total of six Icinga servers.” To Icinga it doesn’t make any difference whether the infrastructure is hosted in a private or public cloud or on premise – Icinga automatically imports data via the network.
The biggest benefit of Icinga is that it has helped Sun Chemical simplify and standardize their monitoring.
Automated and integrated with Service Now
Before, if an IT department at a site would add a new server, they had added it to the monitoring manually. In theory. In practice, it could happen that servers were simply not included in the monitoring at all. “So, I had some servers out that were not monitored,” says Alex Clark. A self-built automation process helped track these servers and add them. “I have a script that runs every week and queries the domains for all domain joint servers and queries Icinga through the API and compares the list. If something is missing it sends me an email.”
Sun Chemical’s monitoring now includes the automatic import of servers and automated generation of checks. With apply rules in Icinga, all Windows servers are set up with a standard set of monitoring checks. For example, all servers need to have an antivirus software installed for security purposes. They also need the software deployment agent installed. All servers need to get security patches every month and the server rebooted for the security patches to get installed fully. All this is now done automatically. For notifications, the manufacturer uses not only email but also ServiceNow as a ticketing system integrated with Icinga.
Success
Trusted Monitoring Solution
Icinga has helped Sun Chemical to get more and more objects into monitoring. It has also enabled he monitoring team to establish rules and automation processes, and the other IT departments to use monitoring to better understand and improve their infrastructure. A big leap came with Icinga Web. The current project at Sun Chemical is to get their monitoring upgraded to the Icinga DB for better speed and scale in Icinga Web.
And more projects are to come: The network department requested a specific kind of dashboard. And besides DB and dashboard integration, Alex Clark wants to eventually get to use the Icinga Director to simplify the creation of pulling mechanism from the Active Directory, drive automation forward and delegate tasks. The Icinga installation in their test environment is the place to try things out.
“I think our main success story at Sun Chemical with Icinga is that now we have standardized our monitoring requirements on all our Windows servers. Before that, the monitoring checks were all over the place. With Icinga 2 we set a standard template to check that our standard requirements are achieved.”
Besides being supported by the knowledge of the open source community and being backed up by professional Icinga support, Alex Clark appreciates the simplicity Icinga has brought to his daily life.
Outcomes
- Simplification and standardization of monitoring
- Enhanced security by establishing high availability set-up
- Automation via Icinga 2 apply rules
- Integration with ServiceNow
- Modern and streamlined design of Icinga DB Web
Tackle Your Monitoring Challenge
Learn about the basics and essentials of Icinga, and start your own Icinga by following our installation course.